Two new Schwing Bioset screw presses replace legacy belt press and help the WWTP save on hauling costs, reduce operation time, reduce wash water usage, and run a cleaner operation.
Written by Tom Welch
The Town of Collierville operates two wastewater treatment plants. The Shelton Road plant, permitted at 3.5 MGD, was looking to improve dewatering performance and started considering different options in 2018. Schwing Bioset worked with the Client and their Representative to assist with sizing of a screw press system and performed a pilot with a mobile unit in May 2019 to determine expected performance.
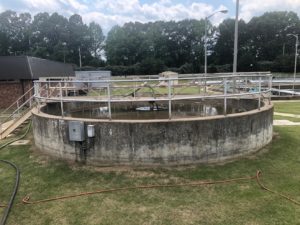
Thickener at Collierville WWTP
This plant currently has a mechanical thickener that thickens a RAS/WAS mixture from +/- 0.5% solids up to 1.5-2.0% solids (see photo below). The existing belt filter press experienced difficulties when attempting to dewater the thin solids at 0.5% and would need a thickener added to the press to achieve acceptable performance. However, height restrictions in the current building precluded this option. The primary goal of the pilot was to confirm that the screw press can successfully dewater the thin RAS/WAS mix around 0.5% solids and then also compare results of the thickened WAS to the performance of the belt filter press.
Upon testing the % cake solids produced by the belt filter press with the thickened sludge, it was determined to be producing 12.4% solids. The screw press model FSP 300 was able to consistently produce cake solids on average above 17.5% for both the un-thickened and thickened sludge. Showing the ability to dewater the thin sludge at 0.55% solids was especially important to confirm that the Schwing Bioset screw press was able to use the thickening zone of the press to successfully dewater the thin material.
The dosage of 36 active lbs./dry ton appeared to be the most effective dosage that provided consistent dry cake and consistent good capture rate. The higher dosage of polymer, 45 active lbs./dry ton, yielded on average 18.85% solids while the lower dosage of 36 active lbs./dry ton yielded on average 17.73% solids. Both results were significantly better than the belt press sludge that was tested at 12.4%, run while incoming % solids of 1.7% solids were fed at the same time, to both the belt press and screw press on the last day of the pilot.
For the new dewatering operation, Schwing Bioset has provided two FSP 603 screw presses to meet a throughput of 550 dry pounds per hour on each press. The supply package also included Boerger rotary lobe feed pumps, UGSI polymer systems, and Valmet inline solids analyzers. Due to thickener operations, there is a wide range of % solids coming to the presses on a daily basis, and from the start of the day to the end of the day.
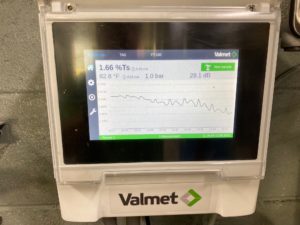
Inline Solids Analyzer Daily Trend
The inline solids analyzer is designed to send an instantaneous signal of % solids of the incoming feed to the press. As the % solids change, the signal is sent to the PLC, which controls the feed pump and the polymer system. The PLC will send signals to the polymer modulation valves and the polymer and make-down water will be controlled based on the instantaneous readings. The inline solids analyzers suggest that the units have the ability to save on average about 25% polymer dosage annually.
During startup of the presses in the fall of 2021, it was noted that there was a variability of incoming % solids ranging from 2.33% down to 1.66%. This automatic control system assists the plant operators as they don’t have to attend the press operations the entire shift and do multiple % feed solids test so that optimum performance can be attained.
Once the performance testing was completed, the plant operation staff were trained by Schwing Bioset Field Service Techs on all aspects of the system. The plant currently hauls the dewatered sludge for disposal at the landfill about ten miles away. Although the landfill tipping fee and hauling costs are presently manageable for the city, it is always a balancing act to determine proper polymer dosage with % cake solids to see how to best operate the presses. Since the previous belt press operation was averaging between 12.5 – 14%, the goal with switching to the Schwing Bioset Screw press technology was to increase the solids and reduce the overall hauling costs.
After several months of operating the equipment, monitoring data, and further optimizations, the plant was able to determine that they could run with 13 pounds of active polymer per dry ton, and routinely average between 16 – 17.5% solids. With a higher dosage of polymer at 22 pounds of active polymer per dry ton, they were able to average around 19% solids. Since the lower polymer dosage resulted in cake solids that were around 4% higher than the legacy belt press operation, it was determined that the overall savings for the plant was to accept lower % cake solids with a significantly reduced polymer dosage. As noted, the polymer dosage during the pilot required a higher dosage than what was determined to be the optimum amount of polymer needed for normal production. A different polymer is now being used, which has offered similar % cake solids, but at a significantly reduced dosage.
The new design has two FSP 603 screw presses. The two machines were designed with one duty/one standby machine with enough capacity to meet current and future demands on the plant. Although the current operation protocol is to run both presses at the same time, there is enough capacity in one machine to operate just one machine at a higher throughput.
Running both machines allows the best % cake solids which saves on hauling costs, and by running both presses, the operation time per day is lower, allowing the operators to address other parts of the plant. Since the screw press can operate unattended the majority of the time, because of the automatic controls of the operation, this gives added flexibility for operations staff. The previous installation had one belt press so there was no redundancy. As the screw presses don’t have continuous wash water like the belt press, the new operation is much cleaner, and the wash water usage is reduced by 90%.
- Legacy Belt Press
- New Screw Presses
- Polymer Systems
- Feed Pumps and Inline Solids Analyzers
Visit our website to read more about our Products, then contact us to learn about this project or find out how we can help your plant too.
Dwonload Our Brochures and Application Reports
Read More Blog Articles From Schwing Bioset